新書推薦:
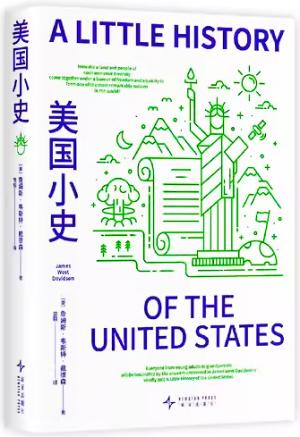
《
美国小史(揭秘“美国何以成为美国”,理解美国的经典入门读物)
》
售價:HK$
81.4
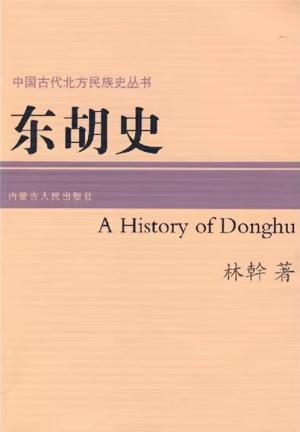
《
中国古代北方民族史丛书——东胡史
》
售價:HK$
87.8
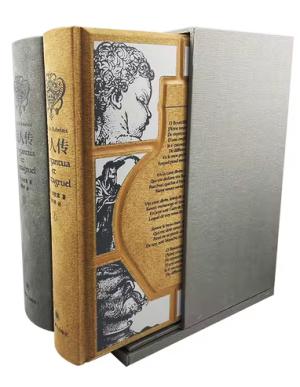
《
巨人传(插图珍藏本)
》
售價:HK$
705.6
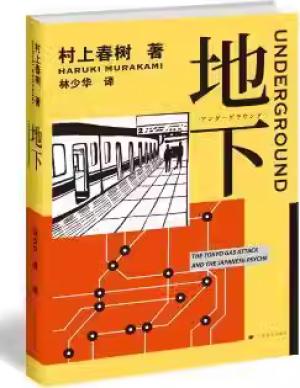
《
地下(村上春树沙林毒气事件的长篇纪实)
》
售價:HK$
76.7
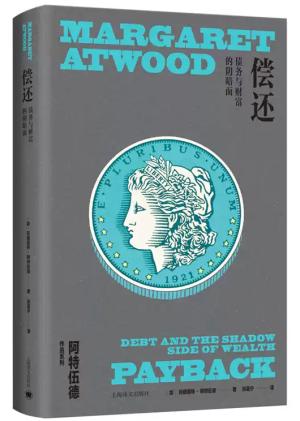
《
偿还:债务与财富的阴暗面
》
售價:HK$
80.2
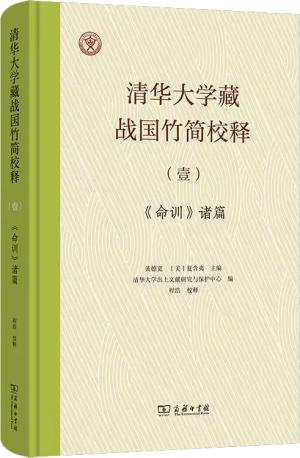
《
清华大学藏战国竹简校释(壹):《命训》诸篇
》
售價:HK$
94.4
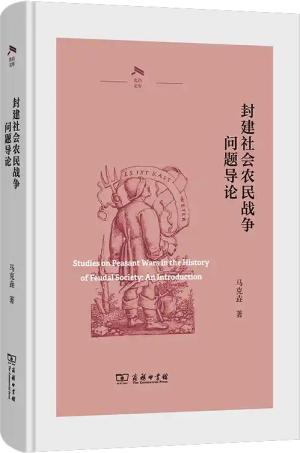
《
封建社会农民战争问题导论(光启文库)
》
售價:HK$
68.4
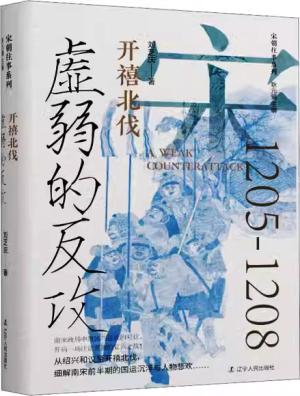
《
虚弱的反攻:开禧北伐
》
售價:HK$
92.0
|
編輯推薦: |
认识系统:理解系统如何运转、理解关注区域的主要流程和影响因素;理解精益的原则方法、理解方法的适用条件。描绘完美:什么才是“好”的?什么又是“不好”的?明确改善的方向,清晰地描绘完美,与相关人员建立起统一的认识。深入和质疑流程:不断地质疑、一步步地深入流程,去发现阻碍实现完美的限制因素。构建方案和实施:走向完美、设定目标状态,针对限制因素和根本原因来构建解决方案,并进行实施。
|
內容簡介: |
本书首先探讨了精益物流的现状,提出了阻碍精益和精益物流实施的主要障碍来自于精益专业能力和领导力的缺乏,尤其是系统化思考和观察能力,并将其具体细化为实施精益的关键能力:认识系统、描绘完美、深入和质疑流程、构建方案和实施;然后参考关键能力的结构,按照销售物流、生产物流、供应物流的顺序,以物流的12个问题为线索,依次讨论了各物流环节的主要关注内容、大致的理想模式、实际运用中的注意事项、对常见问题的讨论、可能的解决方案等,为精益物流的实施提供了实际操作理念和方法;最后针对一些共性的问题,如布局、搬运系统、库位管理、包装等进行了阐述。本书注重系统性和完整性,在结构和顺序上力求清晰地阐述精益物流的关键内容,同时也注意实践性,涉及实施中许多具体的、实际的问题,具有很强的实用性。尽可能做到点面兼顾,既能体现出全面和系统性,也能有一定的细节和深度,对现实活动有直接的指导作用。
|
目錄:
|
前言第1章精益物流概况1.1物流:简单还是复杂?1.2物流的改善空间1.3物流改善的局限1.4精益的吸引力1.5精益物流的规则和方法1.6与传统物流的区别1.7精益物流实施现状1.8什么阻碍了精益及精益物流的实施效果1.9领导力的转变第2章精益物流实施的关键能力2.1认识系统当前的物流系统是如何运转的物流问题的相互关联和影响精益物流工具的适用条件、好处和代价2.2描绘完美什么是浪费完美的流程——发货完美的流程——生产完美的流程——供应完美的关系——合作2.3深入和质疑流程从系统整体来考虑问题:应该关注什么什么是造成问题的原因现场观察,深入流程大胆假设,小心求证量化分析、数据支持2.4构建方案和实施目标状态的设定及设定模型目标状态的针对性和灵活性明确实施策略现场实施效果的验证标准化第3章精益物流实施及改善——销售物流3.1 Q1.客户波动有多大?客户分析的内容什么叫波动?大数定律如何评价波动的影响对产品的区分和策略3.2 Q2.按订单生产还是建立库存?缩短生产前置期的好处按订单生产就好吗?如何应对需求的波动3.3 Q3.客户如何存储、搬运、使用以及下单?客户的真实消耗要求背后的成本,客户清楚吗?下单的不同方式直送上线避免拆包、重包鼓动客户多下单的风险不一致的交货期3.4 Q4.如何向客户送货?提高发货频次客户不在意发货时间的原因客户自提的理由3.5 Q5.成品存储多少,用什么设备,存储在哪里?如何评价成品库存的高低需要高架吗需要托盘吗仓库集中还是分散第4章精益物流实施及改善——生产物流4.1 Q6.连续流从哪道工序开始?什么阻碍了连续流?设备间复杂的对应关系加快流动FIFO大小的确定前后工序的隔离4.2 Q7.如何排生产计划?减弱客户波动的影响稳定对零件的需求均衡生产均衡不适用吗直接按客户需求拉动按什么样的能力排产4.3 Q8.如何触发前道生产?均衡创造了平稳的需求吗消耗控制拉动真在起作用吗拉动的好处非常规品种生产按序生产4.4 Q9.如何向产线供料?向工位的循环供料仓库到生产区域的循环供料与生产线接口的设计及改善库存水平物流量的稳定性和运输利用率第5章精益物流实施及改善——供应物流5.1 Q10.原材料和外购件存储多少,存储在哪里,用什么设备?该存储多少主要零件的直送上线仓库该存储什么5.2 Q11.如何下单给供应商?订单的模式看板的优势需求稳定吗供应商管理库存的误用5.3 Q12.如何安排运输?增加运输频次区域内运输量的整合循环取货5.4供应商发展第6章整合在一起:共性问题的处理6.1现场管理6.2收发货时间窗口6.3存储设备的选择和改善6.4搬运系统的改善6.5库位管理改善6.6布局的改善6.7包装及可回收包装的改善6.8与信息系统的结合价值流图标参考文献后记
|
內容試閱:
|
制造业对于丰田生产方式和精益生产的学习和模仿已经有三十多年的历史了。在我所支持到的工厂中,许多已经有十年左右的精益实施经验,精益思想和工具已经不再是新鲜事物。如果你进入到生产车间,可以看到整洁有序的现场,可以看到醒目的安灯,显示着目标和差异,也许你时而可以听到安灯的警报声和赶忙介入的线长;你可以看到精益生产线,一人多工位的操作,地面上还标明了操作工的移动路线;你可以看到循环供料车拉着多节拖车,在有规律地沿着固定路线行驶;看板循环触发生产,零件存储在超市中;一些零件从供应商直送上线,甚至有的工厂改变了在仓库集中收货的方式,可在生产线边直接收货;均衡也变得普遍了,插着许多看板的均衡板树立在线边。这些改变需要工厂各级别员工的共同努力才能实现,而一系列的改变并持续下来就可形成优势。这些工厂有的已经成为全球关联工厂中的样板,远超过国外具有几十年经验的老厂,这也得益于新工厂更愿意尝试新的方法以及国内员工的高效率和很强的执行力。如果近距离看,你会发现一些问题:生产线操作工之间的工作量有较明显的不均衡,物料摆放不合适,周期重复出现的人等待机器的情况;每小时的损失记录并不完整,主要损失的趋势没有下降;送料车上物料时多时少,利用率不高;线边库存水平如果考虑到补货周期似乎有明显的不合理……如果再和工厂的人员交谈,会发现不少管理人员认为精益就是减少员工,有的甚至准备在改善后就进行裁员;工厂不断地招入实习生来降低成本,导致难以培训高素质的能解决问题的操作工;一些管理者似乎不怎么关注现场中流程的改善,也不花时间现场指导,或者也缺乏对流程的深入理解以及现场指导流程改善的能力,太看重报告中的数据指标;而许多人也不是很清楚这些精益工具在什么条件下使用,真正得到的好处又是什么;有经验的精益支持人员为了职业发展工作两三年就换离岗位,而新来人员缺乏经验难以给予改善项目有力的支持……这么看来,精益的道路只能算是刚刚起步,距离尽善尽美还很遥远。而说到物流方面,这种成熟度就更低:管理混乱,产品即将上线生产,循环供料车的站点还没定下来;方案多是模仿现有的模式,缺乏深入的分析讨论;项目相关人员对于物流方面具体应该考虑什么,怎么考虑,何时考虑并不清楚。什么阻碍了精益的实施效果?是精益专业知识吗?也许是,缺乏专业知识会导致应用的问题;但也许不是,在许多情况下,必要的知识就够了,过深、过多的知识,并不能帮助解决问题。对一些改善工具和方法知道很多,不代表解决问题时更有帮助;对当前流程了解得很详细,不代表能有效解决问题;有很强的执行力和推动力,也不代表效果就会好。所谓木桶原理,某个方面的强项,并不意味着实施效果就会好,这要受到短板的限制。应在一些关键方面达到一个平衡,从而能更有效地面对精益的实施活动。首先是对精益的认识、对生产和物流系统的认识。到底要考虑什么问题,各个问题之间又有什么样的相互关系和影响,这既有助于整体性地理解现状,避免大的疏漏,又有助于在关注局部时,还能顾及和考虑与其相关的问题。质疑是极为重要的。没有质疑就没有改进。质疑是思考、是观察,需要一双挑剔的眼睛,一个积极运转的大脑,关注细节、思考和发现问题。不浮于表面、不泛泛而谈、不光讲大道理,要深入流程地质疑,质疑的同时也更深入理解流程。但不要没有原则、没有方向地质疑。质疑一切又有什么意义?重要的是改善系统和流程。什么才是理想的系统和流程?这会给出改进的方向。对系统的认识也会引导质疑的方向。核心的部分是构建解决方案,但这很可能是自然而然的结果,尤其是在深入流程之后。要具有现场实施的能力,能每日在现场实现小的改进,从而短期内产生大的改变。不了解体系,就是盲人摸象;不理解完美,就缺少方向;没有掌握质疑,就无法深入流程;不深入流程,就无法找出问题根源;缺乏快速实施,就难以产生改变。期望有个标准来简单复制去实施,这可能太过理想化。一个同样的问题,比如生产线的补料,不同的工厂,乃至同一工厂中不同的产品,都可能面对不同的情形。物料尺寸的大小,不同品种间共用零件的占比,会导致补料的细节操作有着非常大的差异。有的产品补料是非常简单的,只是个别零件的补充;有的却是非常复杂的,多数的零件都要被退回。解决方案大体上类似,但细节上却有很大的差异。实施和改善,要基于深入流程、了解具体情况来确定有针对性的方案。感谢在博世公司工作期间同事对我的帮助,从现场观察、项目实施、讨论和反馈、培训和教练等各类活动中,我都受益匪浅。精益之旅是一段非常愉快和充实的工作经历,能够不断学习,不断发现新的空间,而学习和自我发展就是生活的关键组成部分。通过精益工作的不断深入、不断学习,调整自己对待事物、对待人的看法和调整自己的行为,这本身就是非常有趣的过程。由于时间和能力所限,难免有不当和偏颇之处,欢迎交流和批评指正。李震宇
|
|